The Joy of RGB LED Pixels
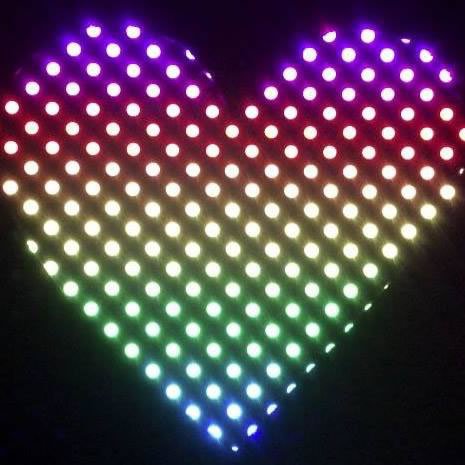
In the 20+ years that I’ve been working with lights embedded in fabric, the available technology has changed dramatically. My early designs were mostly limited to red, green, and amber LEDs (see my sound-reactive handbags and Sit ’n Stare panels from 1999). I was excited when blue LEDs became more affordable, and thrilled to have access to pink/purple options a few years later.
RGB LEDs were another great advancement, making it possible to create a blend of light colors from red, blue, and green emitters placed next to each other on a circuit board, and eventually, within the same lens. Today, modern pixels have a miniature controller associated with each LED, allowing any light in a chain to receive individual instructions via serial communication.
This is a huge game-changer! I wrote this post to share (and explain) my enthusiasm.
simplified wiring and assembly
RGB LED pixels are assembled in chains which transmit power, ground, data, and (sometimes) clock signals to other pixels downstream. You can build and test these chains before installing them in a garment, and all of the soldering can happen far away from the sewing table.
For many of my older installations with single-color LEDs, the lights were mounted in the fabric before they were soldered together. This made testing and troubleshooting a much more delicate process. To animate these LEDs, it was necessary to connect each light (or group of lights wired in parallel) to an output line from the LED controller. This often required a ridiculous number of wires, adding bulk to the garment.
With the older methods, it was possible to create fairly sophisticated chasing patterns and other effects. However, once an LED was physically connected to a group, it would always have to be lit up at the same time as the other lights in that group. For example, if horizontal rows of LEDs were wired together, you could animate the rows in sequence moving up and down, but you would not be able to also do a side-to-side animation, without changing the hardware.
create multiple effects with the same hardware
The ability to control each RGB LED pixel independently is an extremely powerful feature of the newer technology. We can build the piece first and then edit the animation effects later (with very few limits) when the software is customized. This also makes it easier to get client feedback for this part of the design process, since we can share preview videos of the actual lighted garment and adjust the software as needed.
Some decisions are still made in advance, such as the total number of pixels and the physical layout.
This process is so much better than the "old way" that I often recommend RGB pixel-based designs for projects that only need to use one color. When you factor in the amount of labor required, the difference in cost also disappears.
so many colors!
The other features are wonderful, but in the end, it's all about the color. A quick glance at my lighted clothing portfolio (or the paintings on my fine art site) will tell you that I'm a fan of bright colors and rainbows. RGB LED pixels make it so much easier to play with color as a design element of each new piece.
There is one slight down-side: having so many options makes it hard to pick a favorite color combination or animation effect. Fortunately, we can include a long list of pre-programmed modes in the software, and the wearer can change the color or effect to match the occassion.